Spiral Wound Boiler Waterwalls
A global oil and gas leader utilized Gecko Robotics’ robust inspection data to save over one million dollars in replacement costs.
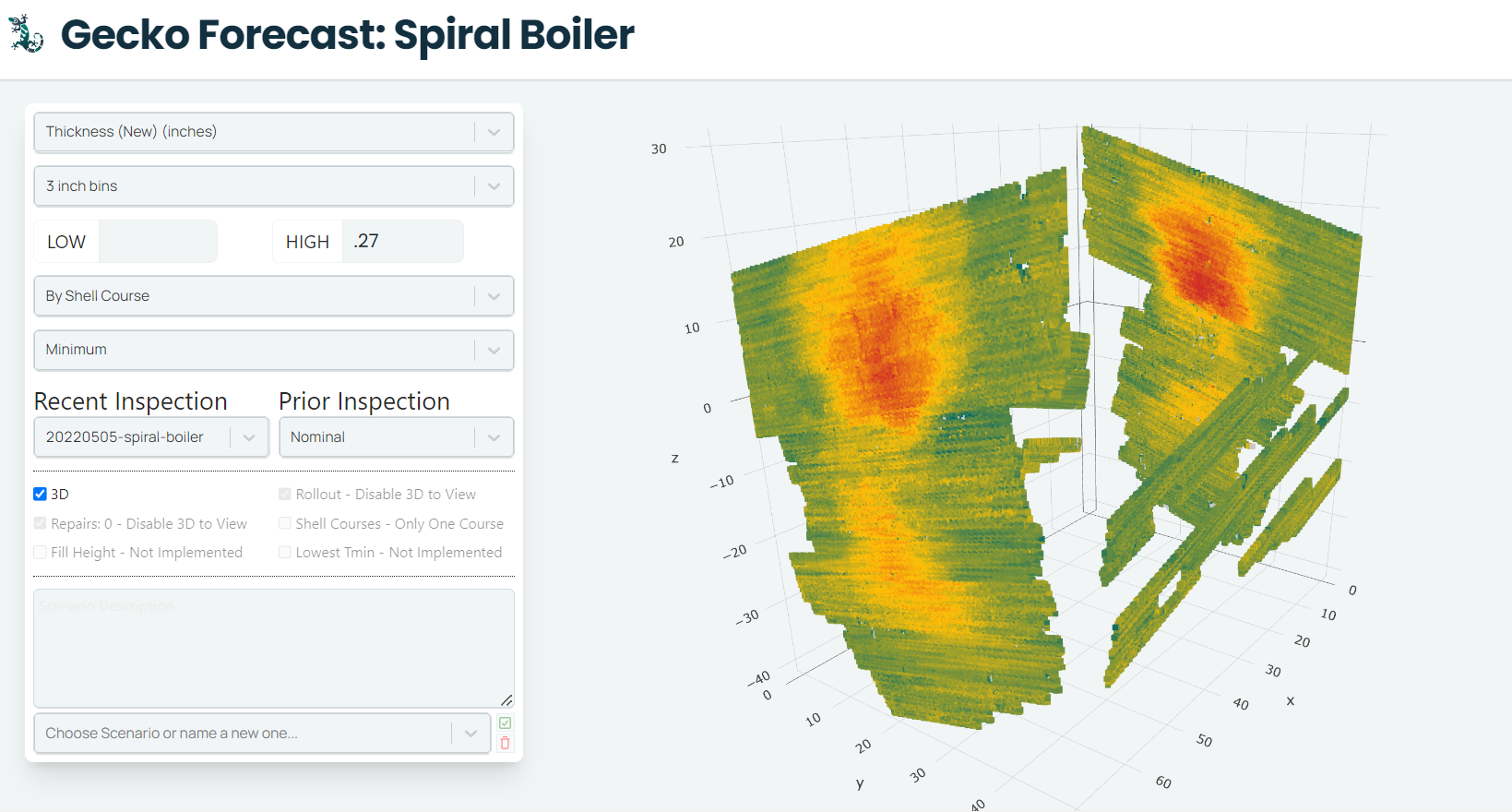
Challenge
- Manual inspection of a spiral wound boiler with multi-lead rifle tubing left large gaps in coverage
- Conventional UT cannot effectively differentiate the wall thickness between the ribs and gaps of internal rifling
- A potential tube lead could cause forced outages and wall replacement costs totaling upwards of $5 million
Solution
- Full-coverage Rapid Ultrasonic Gridding (RUG) inspection using TOKA® 4 robotic platform
- Gecko Portal® software
Result
- No scaffolding or dedicated company resources required
- Nearly 15 million UT data readings obtained
- Saved the plant several million dollars in replacement costs by pinpointing areas in need of repair
- RUG's specialized narrow beam immersion transducers reliably differentiated between rib and gap thickness to provide accurate UT readings